Oaks ’n’ Folks – Volume 17, Issue 2 – August 2001
California has the potential to become an important hardwood lumber producer. It has a high demand for hardwood lumber from manufacturers and consumers, skilled timber and woodworkers capable of producing the lumber, an underutilized resource of high-density hardwoods, and many rural economies in need of new businesses. Yet, the California hardwood sawmill industry remains a fragmented, loosely connected organization of small producers with significant processing and economic challenges. As a result, California meets most of its demand for hardwood lumber with imports from the eastern U.S. or other countries. Currently, a large number of hardwood trees are removed in connection with urban development, hazard tree removal, or forestland conversion. Much of this hardwood fiber is sold as low-value firewood or pulp chips or ends up as landfill. In addition, if the native hardwoods succumbing to Sudden Oak Death syndrome can be used for lumber, then even more opportunities will open up to utilize large quantities of native-grown hardwoods.
Tanoak (Lithocarpus densiflorus), one of the species most susceptible to Sudden Oak Death disease, is one of the few hardwood species native to California that meets the three major requirements of a viable resource for commercial lumber and value-added products:
- Tree and wood property characteristics that are favorable to lumber and wood products.
- A sufficient standing tree inventory to sustain harvesting volumes needed to meet economic requirements of sawmill production.
- Trees are concentrated in regions with an existing harvesting infrastructure.
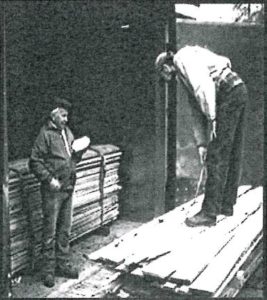
Over the course of history tanoak has gone from a tree valued only by the west coast leather tanning industry, to weed species status, to finally, recognition of some of its unique wood properties. Tanoak received this common name because of its importance to the early leather tanning industry in the west. The high tannic acid content of its bark made it the favored species for extraction of tannin, the natural chemical used to tan leather. By 1907, the use of tanoak for tannin was subsiding because it was becoming harder to find the large tanoak trees needed for favorable economic returns and the tanning industry was beginning to switch to synthetic tannins. By the early 1960’s, only a few natural tannin operations remained in California. Although the market for tannin has disappeared, there are other use options. Because tanoak exhibits very good machining and finishing characteristics and because of its high density (40.4 lbs/ft3 at 8% moisture content) and hardness, it can be an excellent choice for high quality furniture and flooring. It compares favorably in physical properties to nor-thern red oak, a benchmark furniture species.
The U.S. Forest Service estimates the size of the tanoak resource to be more than 2 billion cubic feet of standing timber. It has been estimated that an annual harvest of about 50 million board feet could be sustained on the non-industrial private forestlands of the northern California coast region.
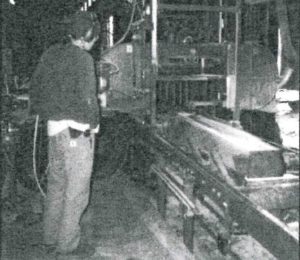
In spite of tanoak’s favorable characteristics and relative abundance, a long-term tanoak industry has not materialized. A lack of information on processing characteristics and recommended manufacturing techniques continue to be a problem for efficient cost- effective production. In addition, a thorough understanding of the expected lumber recovery and grade yield from the available resource is needed to understand the economic viability of tanoak lumber production. To help address these needs, a multi-year project was initiated by the University of California Forest Products Laboratory to develop recovery, yield, and processing information on the manufacturing of lumber from tanoak in northwest California forestlands. The information gathered from this project will also be of value to small mill operators working with non-commercial timber resources.
Each selected tree and the logs produced from the trees were measured in size and form (shape), and estimates were made of the lumber volume expected from each tree or log. The trees, logs, and lumber produced were also graded following standard hardwood grading rules. After the logs were processed into lumber, various combinations of ambient air, steam-heated kiln, and dehumidification kiln drying methods were used to study the effect of drying temperature and rate of drying on the quality of the lumber. One-half of the lumber from each site was kiln dried directly from the green condition to 8% moisture content, and the other half was first air dried to 20% and then kiln dried to 8% moisture content.
Lumber Yield Estimations are Reasonable
A total of about 50 thousand board feet of lumber (green basis) was produced from the two sites. The trees from the MHDA site were larger and of a higher grade than those from the ISF site. At the MHDA site, 42% of the trees were measured as tree grades 1 and 2 (1 being the highest grade, 3 being the lowest) with an average diameter at breast height (DBH) of 24 inches. Only 16% of ISF trees were measured as grades 1 and 2, and they averaged an 18-inch DBH. The average defect deduction in trees from both sites ranged from 10 to 15%. The Girard Form Class method, based on the size and taper of trees, provided a reasonable estimate of the lumber yield; however, it overestimated the volume of 1-inch thick (4/4) dry lumber by 19% and underestimated the yield of 1 1/4-inch thick green lumber by 23%. The two best common log-based estimation methods for predicting lumber yield on the basis of log size and taper were the International 1/4-inch log rule method, which overestimated dry lumber yield by 11%, and the Doyle method which underestimated yield by 9% (Figure 1).
The yield of green lumber from the tanoak study logs was similar to yield expected for commercial eastern hardwood species. The top log grade yielded 68% of No. 1 Common or Better lumber (the two most valuable grades). In the middle and lowest log grades, 49% and 31% of the lumber produced was in the upper grades, respectively.
Drying Proves to be Problematic
Drying results from the study indicate a potentially serious drop in grade, and hence lumber value, when the lumber is dried (Figure 2). The major drying defects encountered were cell collapse, warp, and a drying-induced chemical discoloration of the wood (chemical stain). There was a 30% decrease in the volume of No. 1 Common or Better lumber from the green condition to the kiln dried condition (dry without stain) due to cell collapse and warp. If the chemical stain was counted as a defect, which it should be, then the drop in the volume of upper grade lumber was 78%. This is clearly an unacceptable amount of degrade. Air drying the lumber for 6 months before kiln drying dramatically reduced the amount of warp and collapse; however, stain remained a problem.
It was noted that drying degrade was greater in the lumber produced from the older-larger trees in the study. A strong correlation was noted between the amount of cell collapse in the lumber produced from these trees and the high frequency of “mineral streak/heart stain”, a zone of dark reddish-brown discoloration visible in freshly cut lumber. It was noted during the field trials that the lumber from the MHDA site appeared to have a higher incidence of “mineral streak/heart stain” than the ISF material. It was also evident that severe drying defects were almost always present in the zones of this “heart stain”.
A study conducted at the University of California Forest Products Laboratory in 1965 found a higher incidence of heart stain in older trees with slow growth rates. In the 1965 study, there was no apparent trend between heart stain and diameter, but trees less than 80 years old had less heart stain than trees over 100 years old. When growth rates were compared, the trend was strong—faster growing trees exhibited the least amount of heart stain (20%) and the slowest growing trees had the most (43%). The field observations in the current project are consistent with these observations. Further study is needed to understand the mechanism of heart stain formation and its effect on drying defects.
Summary
Tanoak has the potential to be an important hardwood resource. However, some of its unique wood properties present manufacturing challenges that require specialized techniques and extra care, especially during drying. In this study it was confirmed that tanoak is prone to warp, collapse, and discoloration (staining). The knowledge gained from the results of the study help to understand the manufacturing challenges and in developing recommendations for maximizing lumber yield and value.
The importance of following good drying practices cannot be overemphasized. It is necessary to minimize the defects created as the lumber dries to achieve the full product value. The best results are obtained with partial air drying followed by kiln drying, but with care, good results can also be obtained by immediately drying from the green condition in a kiln. Based on the results of the study discussed in this article, the recommended drying practices are as follows:
- Process logs into lumber as quickly as possible because stain is more likely in logs stored longer than 1 month.
- Fresh cut lumber must be stacked immediately on stickers to start the drying process.
- The initial drying conditions (for at least the first two weeks of drying) should encourage good circulation of air at a temperature between 90 and 100 °F with a relative humidity between 70 to 80%. This can be accomplished by either air drying or kiln drying methods. If it is not possible to maintain these air conditions, then it is important to keep the temperature below 80 °F to minimize drying-induced chemical discoloration.
- Maintain the above conditions until the average lumber moisture content reaches 30% and then gradually (over a period of 3 weeks) increase the drying conditions in the kiln to a temperature of 140 °F with a relative humidity of 30%.
- Dry the lumber to 6 to 8% moisture content for inland locations and 8 to 10% for coastal climates.
Tanoak certainly has utilization value. It is being increasingly accepted as hardwood flooring and furniture stock in both commodity and niche markets. Creating new markets or competing in existing wood markets with well-established species is never easy, so it is extremely important to keep manufacturing costs as low as possible by doing everything right the first time. The University of California Forest Products Laboratory is willing to help.
This project received support from the U.S. Forest Service, Region 5 State and Private Forestry and the cooperation of two north coast nonprofit organizations, the MHDA and the ISF.
For more information visit the UC Forest Products Laboratory web site at http://www.ucfpl.ucop.edu or contact John Shelly by email, john.shelly@ucop.edu, or by phone, (510) 215-4210.
John R. Shelly
CE Forest Products Advisor, UC Forest Products Laboratory
prepared and edited by Adina Merenlender and Emily Heaton